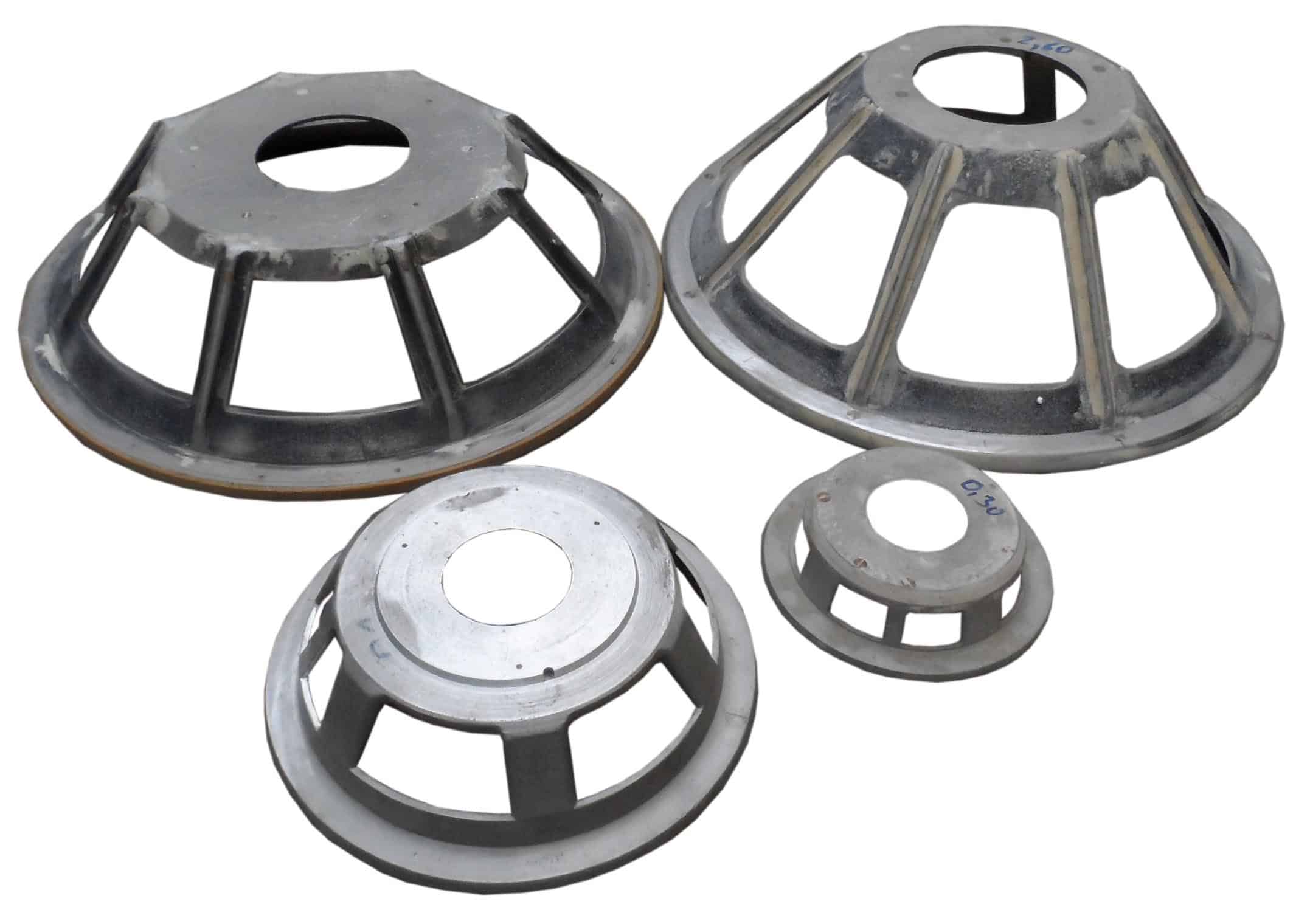
Kosz, czyli na ogół metalowa rama, do której mocowana jest membrana z zawieszeniami i obwód magnetyczny.
Niewątpliwie niezbędnym – i kto wie, czy nie najważniejszym elementem każdej aparatury nagłaśniającej – są przetworniki elektroakustyczne, czyli mówiąc popularnym językiem: głośniki. To one w znacznym stopniu decydują o jakości brzmienia zestawu nagłaśniającego i to niezależnie od jego wielkości, mocy i miejsca, w którym będzie wykorzystywany. Na niewiele zdadzą się nawet najbardziej wymyślne konstrukcje paczek napędzanych supernowoczesnymi wzmacniaczami, z wykorzystaniem zaawansowanych procesorów głośnikowych, jeśli sygnał będzie finalnie trafiał do przetworników, w których pękają membrany, cewki odklejają się od membran, a uzwojenia od karkasów, pozostając w szczelinach obwodów na pamiątkę radosnej twórczości producenta lub majstra, który podjął się naprawy przetwornika, mając o tym jedynie bardzo blade pojęcie.
Ten krótki opis nieszczęść oczywiście nie wyczerpuje wszystkich możliwych usterek, więc w cyklu kilku artykułów zajmę się każdym elementem głośnika z osobna i postaram się przybliżyć czytelnikom zagadnienia związane z ich uszkodzeniami i serwisowaniem. Te kwestie od zawsze wzbudzały wiele wątpliwości i narosło wokół nich mnóstwo mitów, z którymi trudno walczyć, szczególnie w epoce Internetu, gdzie każdy może pisać w dowolnymi miejscu cokolwiek, co tylko przyjdzie mu do głowy. Osobom niezorientowanym w subtelnościach tematu trudno się czasem połapać w tym natłoku informacji i rozstrzygnąć we własnym zakresie, co jest rzetelną informacją, a co rojeniami jakiegoś mniej lub bardziej anonimowego „specjalisty”. Często jest tak, że te porady przypominają działania znachorów, o których ostatnio zrobiło się głośno, choć w przypadku głośników na szczęście możemy mówić jedynie o stratach natury finansowej.
Oczywistym jest, że wiele awarii głośników wynika z nieprzestrzegania zasad prawidłowej eksploatacji aparatury, ale obserwuję również w ostatnich latach znaczący wzrost uszkodzeń powstałych z ewidentnej winy producenta i dotyczy to również sprzętu z wyższej półki, za który odbiorcy płacą niemałe pieniądze. Coraz częściej producenci mamią klienta głównie opakowaniem, a gdy już zajrzymy do środka paczki, to okazuje się, że użyte przetworniki to produkt klasy budżetowej, często no-name, nie licujący z renomą firmy i z pewnością nijak się mający do często wyśrubowanej ceny wyrobu.

Kompletny głośnik o średnicy 15” zmontowany na koszu odlewanym w formie piaskowej.
Ponad dwadzieścia lat doświadczeń w temacie głośników
Do napisania niniejszego artykułu skłoniło mnie między innymi to, że praktycznie niemal od początku mojej działalności (czyli od około dwudziestu lat) sam wytwarzam głośniki i ich wszystkie komponenty, o czym można było również przeczytać w rocznicowym artykule o mojej firmie, zamieszczonym w ubiegłorocznym, marcowym numerze MiT. Nie jest zatem czymś wyjątkowym, gdy dowiaduję się, że niektórzy klienci nadal użytkują mój sprzęt, który zakupili w początkach działalności firmy, a to oznacza, że niektóre wykorzystywane w nim głośniki pracują od blisko dwóch dekad. Dlatego jestem przekonany, że wiem, jak powinien być wykonany dobrej klasy głośnik i jak należy się z nim obchodzić, żeby służył długo i bezawaryjnie. A skoro tak, to mogę się tą wiedzą z Państwem podzielić i w tym celu napisałem trzyczęściowy cykl artykułów, który będzie ukazywać się w kolejnych wydaniach „Muzyki i Technologii”. Celowo pominę w nich aspekty teoretyczne, bo na temat głośników napisano już wiele prac naukowych i osoby zainteresowane mogą bez większego problemu dotrzeć do tych opracowań. Skupię się głównie na kwestiach praktycznych, które z punktu widzenia przeciętnego użytkownika są najważniejsze.
Zacznę zaś od dwóch bardzo istotnych elementów konstrukcyjnych każdego przetwornika, czyli od kosza i mocowanego na nim obwodu magnetycznego. W następnym odcinku zajmę się cewkami, a w ostatnim membranami i zawieszeniami oraz postaram się udzielić kilku rad i praktycznych wskazówek odnośnie zasad eksploatacji i prostych napraw głośników we własnym zakresie, choć od razu uprzedzam, że generalnie jestem sceptycznie nastawiony do działań nieprofesjonalistów w tej dziedzinie.

Współczesny kosz głośnikowy wykonywany w formie wtryskowej, dzięki której możliwe jest nadanie mu nawet najbardziej wymyślnego kształtu. Na prezentowanym modelu kosza widoczne są przepusty chłodzące.
Kosze głośnikowe – podstawa konstrukcji przetwornika
Pisząc o wykonywaniu wszystkich części składowych moich głośników, miałem na myśli każdy jego element oprócz magnesu, a jednym z nich jest oczywiście kosz, czyli na ogół metalowa rama, do której mocowana jest membrana z zawieszeniami i obwód magnetyczny.Piszę „na ogół”, bo produkowane są również głośniki z koszami z tworzyw sztucznych, ale w praktyce estradowej praktycznie się ich nie spotyka.
Kiedy zaczynałem „bawić się” w wytwarzanie głośników, nie było mowy o zakupie gotowych koszy aluminiowych (lub wykonywanych ze stopów metali lekkich), bo większości fabryk na Dalekim Wschodzie, które zarzucają teraz rynek swoimi produktami, nie było jeszcze nawet w planach, a wiele firm, nawet tych dość znanych, odlewało kosze głośnikowe podobną metodą, jak robiłem to ja. Niektórzy producenci wykonują je tym sposobem również współcześnie, choć dziś przeważnie używa się do tego celu form kokilowych lub takich, które pozwalają na wtrysk płynnego metalu pod ciśnieniem, co jest metodą najbardziej zaawansowaną technicznie i najdroższą. Ja stosowałem (i w razie potrzeby nadal stosuję) jedyną dostępną dla mnie finansowo technologię odlewów piaskowych, która jest metodą najbardziej prymitywną, ale jednocześnie najbardziej rozpowszechnioną, jeśli chodzi o produkcję małoseryjną.
Aby odlać kosz głośnikowy tą metodą, należy oczywiście wykonać jego model, który jest niemal identyczny jak gotowy produkt, ale musi uwzględniać specyfikę technologii odlewania (jak choćby skurcz metalu po jego ostygnięciu) i zazwyczaj konieczne jest wprowadzenie pewnych korekt po pierwszych próbach odlewania. Z kolei wykonanie modelu wiąże się z zaangażowaniem dobrego tokarza, frezera i z dopieszczeniem go ręczną obróbką, gdyż pewnych prac nie da się wykonać przy pomocy obrabiarek (albo jest to bardzo kłopotliwe). Materiałem wyjściowym do wykonania modelu jest walec aluminiowy o średnicy i wysokości kosza, z odpowiednimi naddatkami. Często wykonuje się go również metodą odlewania, bo w ofercie handlowej nie występują raczej gotowe wałki o tak dużych średnicach, jakie wymagane są dla większych głośników estradowych.
Dodam jeszcze dla porządku, że czasem można po prostu zaadaptować do swoich potrzeb jakiś istniejący kosz (też tak robiłem), ale oczywiście zawsze będzie to wymagało dostosowania modelu do technologii odlewania i na ogół nie da się przystosować do tego celu koszy innych niż te, które wykonywane są w technologii odlewów piaskowych. Produkcja tego typu koszy wymaga oczywiście współpracy z odlewnią metali nieżelaznych, więc tylko jako ciekawostkę podam, że ponad rok zajęło mi znalezienie takiej, której właściciel podjął się tego nietypowego zadania i potem przez wiele lat korzystałem z jego usług, wzbogacając moją ofertę o kolejne głośniki o średnicach od 6,5” do 18”.
Kosz odlewany w formie piaskowej wymaga nie tylko złożonej obróbki tokarskiej po jego odlaniu, ale również pracochłonnej ręcznej obróbki pilnikiem, bo na odlewach zawsze zostają naddatki, których nie da się usunąć w inny sposób. W moim przypadku i w tamtych czasach nie była to jakaś fanaberia czy przerost ambicji, tylko po prostu konieczność, bo koszty wykonania formy kokilowej (nie mówiąc o ciśnieniowej) były zdecydowanie poza moim zasięgiem. Tym bardziej, że potrzebowałem nie jednej, ale co najmniej kilku, a modeli do odlewania piaskowego udało mi się wykonać i wdrożyć bodaj osiem. Warto może jeszcze dodać, że każdy typ kosza wymagał wykonania szablonu do wiercenia otworów mocujących zarówno obwód magnetyczny do kosza, jak i sam kosz do obudowy, aby zapewnić ich powtarzalność i centryczność w każdym odlanym i poddanym wcześniejszej obróbce mechanicznej egzemplarzu.

Rodzina modeli koszy głośnikowych: największy to kosz osiemnastocalowy w wersji głębokiej i płytkiej, dalej znajdują się dwa modele koszy piętnastocalowych (płytki i głęboki), kosze dwunasto- i dziesięciocalowy. Najmniejszy model ma średnicę 6,5” – wykonany był na konkretne zamówienie klienta.
Diabeł tkwi w szczegółach
Ktoś mógłby zapytać, czy taki kosz w czymś ustępuje ładnemu, gładkiemu produktowi, który powstaje w formie wtryskowej. Odpowiadam więc, że o ile wykona się odpowiednią obróbkę tokarską, czyli z tzw. jednego zamocowania, przetoczy się istotne dla pracy membrany i zawieszeń płaszczyzny, to czasem można uzyskać lepsze efekty niż te, które powstają na wtryskarkach. Miałem kiedyś w ręku fabrycznie nowe kosze odlewane ciśnieniowo przez jakiegoś „chińczyka”, które położone na równej płaszczyźnie kiwały się jak pijany mistrz jednej ze szkół kung-fu, co oczywiście zupełnie je dyskwalifikowało. Sądzę jednak, że pewnie w końcu skuszę się na odpowiedniej jakości produkt dalekowschodni i wykonane kiedyś modele pozostaną już tylko pamiątką i dowodem na to, że jak się chce, to można, a jak nie ma innego wyjścia, to nawet trzeba. Odpowiedź na pytanie, dlaczego tyle miejsca poświęcam koszom, jest dość prosta: otóż dlatego, że od tego elementu bardzo dużo zależy, jeśli rozpatrujemy klasę i jakość głośnika. Jeśli np. płaszczyzny klejenia zawieszeń górnego i dolnego nie będą idealnie równoległe do płaszczyzny mocowania obwodu magnetycznego, to nie da się prawidłowo wycentrować cewki w szczelinie, szczególnie wtedy, jeśli tolerancje luzu są niewielkie. O jakich przedziałach tolerancji mówimy? Podam przykład: mój głośnik niskotonowy z cewką o średnicy 4” ma szczelinę 2 mm (największą ze wszystkich, ze względu na dużą nominalną moc), zaś sama cewka, nawinięta na stosunkowo cienkim karkasie z włókna szklanego, ma grubość około 1 mm. Łatwo wyliczyć, że szczelina po obu stronach cewki to 0,5 mm lub mniej, jeśli zastosować nieco grubszy drut nawojowy.
Wiele tzw. budżetowych głośników ma, niestety, zbyt dużą szczelinę między trzpieniem a nabiegunnikiem, co powoduje znaczny spadek natężenia pola magnetycznego i w konsekwencji spadek skuteczności przetwornika. Taki głośnik łatwiej jest zmontować, ale to jedyna jego zaleta.Oczywiście wielu wytwórców stosuje zamiast koszy odlewanych tańsze, wytłaczane na prasach z blachy stalowej. Niektórzy producenci montują na takich koszach duże, ciężkie obwody magnetyczne, co oczywiście jest błędem w sztuce i często prowadzi do uszkodzeń głośników, gdy kosz nie jest w stanie zapewnić odpowiednio stabilnego położenia magnesu. Dodatkowym problemem może być mocowanie takiego głośnika w obudowie, której najmniejsza nierówność może spowodować zwichrowanie kosza i w konsekwencji zacieranie cewki. Generalnie można powiedzieć, że głośniki wyższej klasy niemal zawsze mają ramy odlewane ze stopów aluminium, magnezu i tym podobnych materiałów – i to niezależnie od ich średnicy. Z drugiej strony oczywistym jest, że samo zastosowanie takiego kosza jeszcze nie przesądza o klasie przetwornika, bo spotykałem już głośniki, w których jedynym wartościowym podzespołem był właśnie aluminiowy kosz, a całą resztę można było bez żalu wyrzucić do… kosza!
Kończąc temat koszy głośnikowych, dodam jeszcze, że ich zewnętrze wymiary są znormalizowane i podawane zazwyczaj w calach, choć gwoli ścisłości trzeba powiedzieć, że bywają również głośniki o średnicach nietypowych. Oczywiście drobne odchylenia od standardowej średnicy zewnętrznej są dopuszczalne, a zdarza się, że kształt zewnętrzny kosza nie jest wcale idealnie okrągły. Nie podlegają natomiast żadnej normalizacji inne wymiary ramy, czyli jej wysokość oraz średnice, gdzie klejone są resory, otwory mocujące itp. Z punktu widzenia użytkownika najbardziej istotne jest jednak to, że występują dość znaczne różnice w średnicy montażowej, czyli tej, która interesuje nas, gdy montujemy głośnik w konkretnej obudowie. Przed ewentualną wymianą przetwornika na inny zawsze warto sprawdzić, czy średnica podawana w katalogu firmowym odpowiada wielkości otworu w posiadanej paczce. Jeśli jest większa, to otwór można oczywiście powiększyć, co bywa jednak kłopotliwe i pracochłonne, ponieważ jedyną metodą jest w tym wypadku użycie pilnika do drewna albo tarnika zamocowanego na wiertarce. Gorzej, gdy kosz nowego głośnika jest tak skonstruowany, że jego wewnętrzna średnica jest znacznie mniejsza niż istniejący w obudowie otwór. Może się wówczas okazać, że po prostu nie będzie go jak umocować, bo otwory pod śruby trafią w powietrze. Dla celów poglądowych prezentuję na fotografii rodzinę modeli koszy głośnikowych, które wykorzystywałem w mojej produkcji. Największy to kosz osiemnastocalowy w wersji głębokiej i płytkiej, dalej znajdują się dwa modele kosza piętnastocalowego (również płytki i głęboki), kosze dwunasto- i dziesięciocalowy, a najmniejszy sześcioipółcalowy, który wykonany był pod konkretne zamówienie, bo klient miał już gotowe firmowe tuby, do których nie udało mu się zamówić w fabryce głośników spełniających jego dość specyficzne wymagania. Na kolejnej fotografii mamy kompletny głośnik piętnastocalowy z magnesem 180 mm, zmontowany na odlanym koszu, ale malowanym proszkowo na kolor czarny, co oczywiście ma znaczenie wyłącznie estetyczne. Pokazuję również współczesny kosz wykonywany jako wtrysk ciśnieniowy, co umożliwia nadanie mu praktycznie dowolnych, nawet najbardziej wymyślnych kształtów.

Próby klejenia roznitowanego obwodu przy pomocy żywicy to kiepski pomysł…
Obwody magnetyczne – na co warto zwrócić uwagę i za co odpowiadają
Obwód magnetyczny to najdroższy element głośnika – składa się na to koszt magnesu (który przeważnie ma formę pierścienia z otworem w środku) oraz dwóch stalowych nabiegunników. Pierwszy z nich stanowi całość z trzpieniem, a drugi jest po prostu płytką stalową z otworem, którego wewnętrzna średnica stanowi zewnętrzny wymiar szczeliny. W tejże szczelinie koncentruje się pole magnetyczne. Co prawda obecnie stosowane są obwody o innej konstrukcji, również będące opatentowany mi rozwiązaniami poszczególnych producentów, ale ja skupię się na modelu podstawowym, stosowanym w ogromnej większości wyrobów dostępnych na rynku. Obwód magnetyczny powinien być wykonany ze stali o jak najniższej zawartości węgla (niskowęglowej), a za ideał pod tym względem uznaje się materiał o handlowej nazwie Armco. Niestety, jest on bardzo drogi i różnica w cenie między „zwykłą” stalą a Armco jest mniej więcej taka jak między magnesem ferrytowym a neodymowym. W swoim czasie korzystałem również z tego materiału i dodatkową trudnością było to, że tokarze go nie lubią, bo jest kłopotliwy w obróbce. Umożliwia jednak uzyskanie większej wartości indukcji w szczelinie, co oczywiście ma wpływ na skuteczność głośnika, czyli tego parametru, który w prospektach opisywany jest jednostkach dB SPL.

Trzpień w kształcie litery T, koncentrujący pole magnetyczne w obszarze uzwojeń cewki.
Zarówno trzpień, jak i nabiegunnik muszą być wytaczane z dużą dokładnością, a następnie pokrywane odpowiednią powłoką galwaniczną, najczęściej jest to cynkowanie. W przypadku moich obwodów dopuszczalne odchyłki w procesie toczenia wynoszą 0,05 mm i przy okazji warto wiedzieć, że mimo znormalizowanych wymiarów cewek głośnikowych, każda firma wykonuje je według własnych standardów, w związku z powyższym ich faktyczne wymiary różnią się i są specyficzne dla danego producenta, o czym szerzej napiszę za miesiąc.

Obwody magnetyczne dostosowane do magnesów o trzech różnych średnicach: 157, 180 i 220 mm. Środkowy pokazany jest z ustalaczem, który służy do precyzyjnego wycentrowania szczeliny między trzpieniem a nabiegunnikiem.
Obwód magnetyczny to drogi element, szczególnie wtedy, gdy zależy nam na dużej mocy głośnika. Co prawda w przypadku stosowania magnesów neodymowych, stali do jego wykonania potrzeba dużo mniej, ale za to koszt samego magnesu wielokrotnie przekracza koszt magnesu ferrytowego, więc kółko się zamyka. Firmy stosują różne „patenty” w celu uzyskania jak największej wartości indukcji w szczelinie, co w prosty sposób przekłada się na skuteczność głośnika. W tym celu wykonuje się na przykład trzpień w kształcie litery T, co pozwala lepiej ukierunkować pole właśnie w obszar pracy cewki i taki obwód pokazuję na fotografii. Jak widać, trzpień w tym wypadku ma dwie różne średnice, czyli jest szerszy w górnej części, przy czym ten fragment ma dokładnie taką wysokość jak nabiegunnik, co zmniejsza efekt rozmycia pola i tym samym zwiększa jego natężenie w szczelinie, w której porusza się cewka. Tych sposobów jest oczywiście więcej, ale na ich dokładnie omówienie nie starczyłoby tutaj miejsca. Warto jednak dodać, że bardzo ważną kwestią jest precyzyjne sklejenie samego obwodu (przed jego namagnesowaniem), czyli w taki sposób, aby szczelina miała jednakową wielkość na całym swoim obwodzie. Wymaga to wykonania odpowiednich precyzyjnych „ustalaczy” i staranności podczas procesu klejenia oraz oczywiście użycia odpowiedniego kleju, gdyż siły przyciągania biegunów w namagnesowanym obwodzie są bardzo duże i spoiwo musi się im przeciwstawić, a dodatkowo być odporne na temperaturę i w pewnym stopniu na udary mechaniczne. A skoro o klejeniu mowa, to warto zauważyć, że czasem zdarzają się awarie głośników spowodowane właśnie odklejeniem się magnesu od nabiegunnika. Powoduje to zakleszczenie i na ogół destrukcję cewki i naprawa często okazuje się nieopłacalna (szczególnie w przypadku produktów budżetowych), bo wymaga demontażu głośnika na czynniki pierwsze i ponownego sklejania i centrowania obwodu magnetycznego. Jest to bardzo kłopotliwe (choć możliwe), a remont najbardziej utrudnia fakt, że obwód jest namagnesowany i nawet jeśli mamy ustalacz dostosowany do danego typu głośnika, to i tak nie da się go wsunąć w szczelinę, więc na dobrą sprawę należałoby go wcześniej rozmagnesować i po sklejeniu namagnesować powtórnie. Jak wspomniałem, siły, które działają na namagnesowane nabiegunniki, są bardzo duże i przy większych średnicach samo oddzielenie płytki od magnesu wymaga często przyłożenia sporej dźwigni. Jeśli nieszczęśliwie podłożymy palec między ferryt a nabiegunnik i coś nam się przesunie, to destrukcja paznokcia może okazać się jednym z mniejszych wymiarów kary…
Dodam jeszcze dla porządku, że czasem spotyka się głośniki, w których górny i dolny nabiegunnik są dodatkowo skręcane między sobą śrubami, lub wykorzystuje się specjalne otwory w magnesach i wówczas można przykręcić obwód do kosza na wylot poprzez magnes, co nieco zmniejsza niebezpieczeństwo ewentualnego rozklejenia.

Poglądowy obraz nierówno sklejonego nabiegunnika – widoczna szczelina o zróżnicowanej wielkości.
Dobry klej to podstawa!
Stosowanie odpowiednich klejów i staranność podczas procesu montażu powoduje, że dobre firmowe głośniki raczej sporadycznie dotykają tego typu awarie. Może się to jednak zdarzyć na przykład w sytuacji, gdy paczka upadnie na twarde podłoże i magnes rozklei się na skutek uderzenia. Taki wstrząs może również spowodować pęknięcie kosza; co ciekawe, narażone są na to bardziej kosze wykonywane w formie wtryskowej, szczególnie wtedy, gdy ich ścianki, ze względów oszczędności materiałowych, są stosunkowo cienkie. Kosz odlewany w formie piaskowej z przyczyn technologicznych musi być bardziej masywny i być może dlatego nigdy nie zdarzyło mi się zetknąć z uszkodzeniem głośnika z powodu rozpadnięcia się tego typu kosza. No ale o koszach już było, więc to tylko taka uwaga na marginesie.
Spotykałem już głośniki, które miały fabrycznie niestarannie i nierówno sklejony obwód magnetyczny, co oczywiście powoduje, że taki głośnik prędzej czy później ulegnie uszkodzeniu, o ile w ogóle zagra. W przypadku produkcji masowej tylko co któreś egzemplarze podlegają kontroli jakości, więc zdarza się, że nawet fabrycznie nowy głośnik jest niesprawny, oczywiście nie tylko z powodu wad montażowych obwodów magnetycznych. Jednak w tym wypadku, jeśli szczelina jest duża, to cewka wprawdzie będzie poruszała się w polu, ale może ocierać o nabiegunnik, co w końcu prowadzi do uszkodzenia uzwojeń, że nie wspomnę o nierównomiernym rozkładzie natężenia pola. Od razu dodam, że taki głośnik praktycznie jest nienaprawialny, chyba że ktoś podejmie się siłowego rozklejenia obwodu i ponownego jego sklejenia, co obarczone jest ryzykiem uszkodzenia magnesu i z punktu widzenia serwisu jest jeszcze gorszą sytuacją niż ta, gdy do naprawy trafia przetwornik z już rozklejonym magnesem. Do celów poglądowych zasymulowałem na zdjęciu właśnie taką sytuację, gdzie wyraźnie widać, że nabiegunnik jest nierówno i niecentrycznie sklejony, przez co szczelina nie jest równa na obwodzie.

Kosze głośnikowe wykonywane we własnym zakresie wymagają również stosowania szablonów wiertarskich, aby zachować powtarzalność i centryczność otworów mocujących.
Wracając do tematu rozklejania się głośników, chciałbym wyraźnie zaznaczyć, że piszę o rozklejeniu się obwodu magnetycznego (ferryt od żelaza) a nie o odklejeniu się całego obwodu od kosza. Ten ostatni przypadek to po prostu „afera”, ale spotykałem już głośniki, których obwody w ogóle nie były przykręcone do kosza, tylko właśnie przyklejone. Można też obwód magnetyczny przynitować do kosza (zamiast przykręcić) i niektórym znanym firmom „chińczyk” właśnie tak robi, a potem klient się dziwi, dlaczego głośnik przestaje grać, choć wcale się „nie spalił”. A wytłumaczenie jest proste: dlatego, że nit puszcza i magnes się przesuwa albo odstaje z jednej strony od kosza, co oczywiście powoduje utratę centrowania i efekty, o których już pisałem. Taki głośnik jest praktycznie do wyrzucenia, bo urwany nit raczej trudno wydobyć z nabiegunnika, a nawet jeśli by się to udało, to nie ma żadnej gwarancji, że kolejny nie zachowa się tak samo. Na jednej z fotografii pokazuję właśnie taki odklejony obwód, który klient próbował przykleić przy pomocy żywicy epoksydowej. Oczywiście to bardzo niemądry pomysł, bo pomijając fakt, że nic to nie dało, to dodatkowo żywica dostała się do szczeliny, w której pracuje cewka, i głośnik – mimo włożonej pracy – nadaje się już tylko do wyrzucenia. A cały problem wyniknął z tego, że wytwórca chciał zaoszczędzić na kilku wkrętach i czasie, jaki jest potrzebny do ich przykręcenia i do nagwintowania otworów w nabiegunniku.
Zawodna technologia nitowania i klejenia dotyczy głównie koszy stalowych, które są stosowane w tańszych głośnikach, choć trzeba dodać, że one również mogą zdecydowanie różnić się jakościowo, na przykład z uwagi na zastosowanie zbyt cienkiej blachy, która nie zapewnia im odpowiedniej sztywności. To tyle, jeśli chodzi o obwody magnetyczne, a na zdjęciu możecie Państwo zobaczyć trzy różne obwody, dostosowane do magnesów o średnicach 157, 180 i 220 mm. Środkowy pokazałem ze wspomnianym wyżej ustalaczem, który służy do precyzyjnego wycentrowania szczeliny między trzpieniem a nabiegunnikiem.
Kończąc pozostaje mi już tylko zaprosić czytelników do lektury kolejnej części poradnika, w której, jak już informowałem na początku, zajmę się cewkami głośnikowymi. Obiecuję, że będzie ciekawie.
Piotr Peto, Muzyka i Technologia
————————————————————————————————————————————————-
Budowa i serwisowanie głośników – cewki głośnikowe
W numerze lipcowym w ramach pierwszej części niniejszego cyklu starałem się wyjaśnić czytelnikom MiT, jak ważne dla jakości głośnika są jego kosz i obwód magnetyczny. Cały drugi odcinek poświęcę cewkom głośnikowym, gdyż jest to ten element przetwornika, który najczęściej ulega uszkodzeniom i wokół tego tematu toczy się chyba najwięcej dyskusji zarówno wśród specjalistów, jak i zwykłych użytkowników sprzętu nagłaśniającego, niezależnie od jego klasy, ceny i producenta.
————————————————————————————————————————————————-
Budowa i serwisowanie głośników – membrany i zawieszenia
W dwóch poprzednich odcinkach cyklu o głośnikach omówiłem konstrukcję koszy, obwodów magnetycznych i cewek głośnikowych, dzisiaj zajmę się membranami i ich zawieszeniami, zwanymi również resorami, zapewne przez analogię do techniki samochodowej. Omówię pokrótce technologię produkcji tych elementów, a potem przejdę do części bardziej praktycznej, bo zdaję sobie sprawę z faktu, że większość czytelników to właśnie praktycy, dla których najistotniejsza jest wiedza pozwalająca na optymalne wykorzystanie posiadanego sprzętu.
————————————————————————————————————————————————-