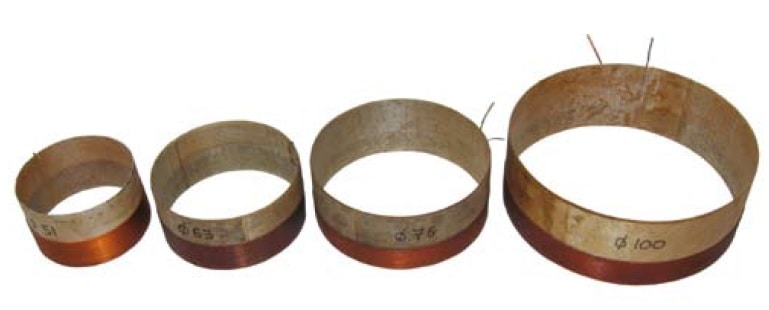
Cewka zawsze stanowi swego rodzaju zagadkę i dopiero po demontażu membrany i zawieszeń można stwierdzić, czy wykonano ją w sposób prawidłowy i czy ewentualną awarię przetwornika spowodowały błędy eksploatacyjne, czy raczej nieprzestrzeganie reżimów technologicznych przez wytwórcę głośnika.
W numerze lipcowym w ramach pierwszej części niniejszego cyklu starałem się wyjaśnić czytelnikom MiT, jak ważne dla jakości głośnika są jego kosz i obwód magnetyczny. Cały drugi odcinek poświęcę cewkom głośnikowym, gdyż jest to ten element przetwornika, który najczęściej ulega uszkodzeniom i wokół tego tematu toczy się chyba najwięcej dyskusji zarówno wśród specjalistów, jak i zwykłych użytkowników sprzętu nagłaśniającego, niezależnie od jego klasy, ceny i producenta.
O ile dość łatwo jest już na pierwszy rzut oka ocenić jakość kosza i obwodu magnetycznego, o tyle cewka zawsze stanowi swego rodzaju zagadkę i dopiero po demontażu membrany i zawieszeń można stwierdzić, czy wykonano ją w sposób prawidłowy i czy ewentualną awarię przetwornika spowodowały błędy eksploatacyjne, czy raczej nieprzestrzeganie reżimów technologicznych przez wytwórcę głośnika. W artykule postaram się więc wyjaśnić, jak powinna być wykonana profesjonalna cewka głośnikowa, i dla kontrastu podam przykłady błędów producentów oraz osób zajmujących się naprawami głośników. Mam nadzieję, że ten materiał rozwieje chociaż część mitów i wątpliwości, a jednocześnie pozwoli czytelnikom mniej zorientowanym w temacie na lepsze w nim rozeznanie. Jest to szczególnie ważne dla tych osób, które inwestują często niemałe pieniądze w aparaturę i z pewnością zależy im na tym, aby jej eksploatacja przebiegała bezawaryjnie i bezstresowo, w czym głośniki odgrywają niebagatelną rolę. Skupię się na najbardziej standardowych, a więc najczęściej spotykanych w praktyce rozwiązaniach technologicznych, choć oczywiście na rynku pojawiają się co jakiś czas rozwiązania nowatorskie, będące wynikiem wytężonej pracy inżynierów czołowych producentów w tej branży.
Spalony głośnik
Określenie „spalony głośnik” jest tak popularne, że wiele osób używa go niezależnie od faktycznej przyczyny zamilknięcia przetwornika. Oczywiście cewka może ulec fizycznemu spaleniu, na przykład na skutek dostarczenia głośnikowi zbyt dużej mocy albo awarii wzmacniacza, który nie ma zabezpieczenia przed pojawieniem się na jego wyjściu napięcia stałego. Takie uszkodzenie skutkuje wychyleniem membrany z cewką w jedno skrajne położenie i na skutek braku chłodzenia oraz przepływu przez cewkę dużego prądu uzwojenie ulega uszkodzeniu. Jeśli taki stan trwa odpowiednio długo, to przekroczona zostaje temperatura, którą jest w stanie wytrzymać izolacja drutu nawojowego (na przykład 180°) i zamienia się on w czarną, zwęgloną masę albo ulega częściowemu spaleniu – co charakterystyczne, często dotyczy to tylko fragmentu uzwojenia. Ten drugi przypadek ma miejsce w sytuacji, gdy głośnik pracuje ze zbyt dużą amplitudą wychyleń membrany i cewka wychodzi poza pole magnetyczne.
Na zdjęciu nr 2 widzimy uszkodzoną w opisany wyżej sposób cewkę głośnika 18″, który według producenta ma moc nominalną 1 kW, choć w tym przypadku to raczej pobożne życzenia niż realne możliwości.
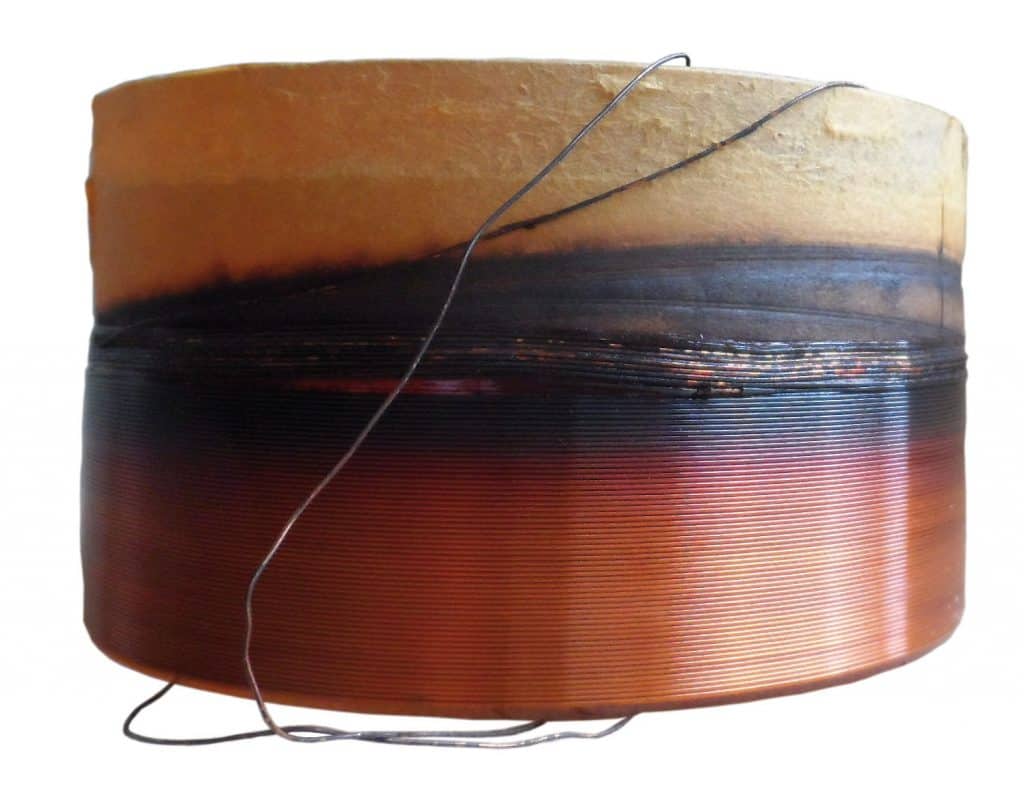
Fot. 2. Przegrzane uzwojenie cewki głośnika niskotonowego dużej mocy.
W przypadku głośników naprawianych przez domorosłych fachowców czasem wystarczy jednak rozgrzać cewkę do normalnej, roboczej temperatury pracy, aby uległa ona uszkodzeniu, a dlaczego tak się dzieje, wyjaśnię w dalszej części artykułu. Jeśli uzwojenie rozsypie się i zsunie z karkasu cewki, to może utkwić w szczelinie, skąd czasem trudno je wydobyć, szczególnie w sytuacji, gdy trzpień nie ma równej średnicy na całej swojej długości. A nawet jeśli to się uda, to nigdy nie ma pełnej gwarancji, że jakaś drobina drutu lub kleju nie ukryje się przed „naprawiaczem” i że za jakiś czas nie spowoduje ponownej awarii wyremontowanego głośnika, dostając się między cewkę a nabiegunnik lub od wewnątrz – między cewkę a trzpień obwodu magnetycznego.
Spaleniu cewek najłatwiej zapobiegać, stosując odpowiednio dobrane do mocy głośników limitery, a także dbając o kondycję wzmacniaczy. Warto również dodać, że uszkodzony głośnik może czasem mieć zwarte uzwojenie cewki (a nie przerwę), co oczywiście skutkuje zwarciem na wyjściu końcówki. Jeśli wzmacniacz nie ma odpowiednich zabezpieczeń na taką okoliczność, również ulegnie awarii, ale w dzisiejszych czasach raczej trudno spotkać tak prymitywne końcówki. Jeśli więc w trakcie imprezy poczujemy charakterystyczny nieprzyjemny zapach (swąd) dobywający się z paczek zasilanych z zewnętrznych wzmacniaczy, to będzie to dowód na to, że głośniki obciążone są zbyt dużą mocą jak na ich faktyczne możliwości. Mimo że profesjonalne cewki w pewnym zakresie są odporne na krótkotrwałe przeciążenia, to jednak jeśli czas ten będzie zbyt długi albo na każdej imprezie będą w ten sposób eksploatowane, to z pewnością w końcu ulegną nieodwracalnej destrukcji.
Efekty zapachowe w trakcie normalnego użytkowania zestawów głośnikowych oczywiście nie są zjawiskiem normalnym, gdyż każda prawidłowo wykonana cewka powinna być wygrzana w procesie wytwarzania w wysokiej temperaturze. Ów proces ma za zadanie utwardzić klej łączący uzwojenia i tylko wówczas, przez kilka minut, możemy poczuć ten charakterystyczny smrodek, którego nie jest w stanie wyeliminować nawet sprawnie działający wyciąg, jak to ma miejsce w moim warsztacie.
Znam jednak z praktyki przypadki, gdy nawet zastosowanie profesjonalnych limiterów, idealnie dobranych do deklarowanej mocy zestawów, nie chroni zamontowanych w nich głośników przed uszkodzeniem. Moce wzmacniaczy rosną nieproporcjonalne w stosunku do realnych możliwości głośników, więc tego typu awarie będą zapewne zdarzać się tym częściej, im bardziej użytkownicy będą bezkrytycznie ufać danym katalogowym, a obecnie wiele firm dla celów marketingowych znacznie zawyża moc przetworników montowanych nawet w zestawach głośnikowych z wysokiej półki cenowej, a nie tylko w sprzęcie budżetowym. Zestawy aktywne ze swej natury są bardziej odporne na tego typu uszkodzenia, bo zazwyczaj producent stosuje w nich dedykowane limitery, optymalnie dopasowane do mocy stosowanych w nich głośników. Często jednak jest tak, że głośnik nie jest spalony, a nie gra albo gra, ale wydobywają się z niego dziwne dźwięki, których nie ma w sygnale sterującym. Istnieje wiele przyczyn takiego stanu rzeczy, które wynikają właśnie z uszkodzeń cewek i teraz postaram się je pokrótce omówić.
Klasyfikacja i przyczyny uszkodzeń cewek
Uszkodzenia cewek można z grubsza sklasyfikować jako wynikające z nieprawidłowej eksploatacji (jak wspomniana już nadmierna moc) i jako niezależne od użytkownika, czyli będące skutkiem nieprzestrzegania reżimów jakościowych przez producenta lub – na co mamy większy wpływ – przez osobę, której powierzamy naprawę naszego sprzętu. Jednak niezależnie od przyczyny awarii, należy wyraźnie podkreślić, że wszelkie usługi w postaci tak zwanego przewijania cewek to w zasadzie półśrodek, bo najlepszym sposobem naprawy głośnika ze spaloną cewką jest wymiana całego układu drgającego, czyli membrany z zawieszeniami i integralnie związanej z nią cewki. Taki remont sprawia, że klient otrzymuje praktycznie nowy głośnik, i to niezależnie od tego, jak długo i intensywnie był on wcześniej eksploatowany. Poważni producenci oferują oczywiście takie komplety naprawcze, choć inną kwestią jest, że czasem każą sobie za nie bardzo słono płacić. Warto wiedzieć, że prawidłowo wklejona w membranę cewka jest niedemontowalna, a wszelkie próby jej wycinania i wstawiania w to miejsce nowej to partyzantka, która nie powinna mieć miejsca w przypadku napraw sprzętu profesjonalnego. Spotykałem już w swojej praktyce przypadki, gdy taka naprawa skutkowała po pewnym czasie oddzieleniem się karkasu cewki od membrany, co oczywiście kończyło żywot tak potraktowanego przez „fachowca” głośnika.
Na zdjęciu nr 3 pokazuję właśnie tak przeprowadzoną niefachową naprawę, gdzie widzimy ogromną ilość żywicy, przy pomocy której ktoś nieudolnie usiłował umocować cewkę w membranie, ale to połączenie zawiodło i cewkę można zupełnie swobodnie wyjąć.
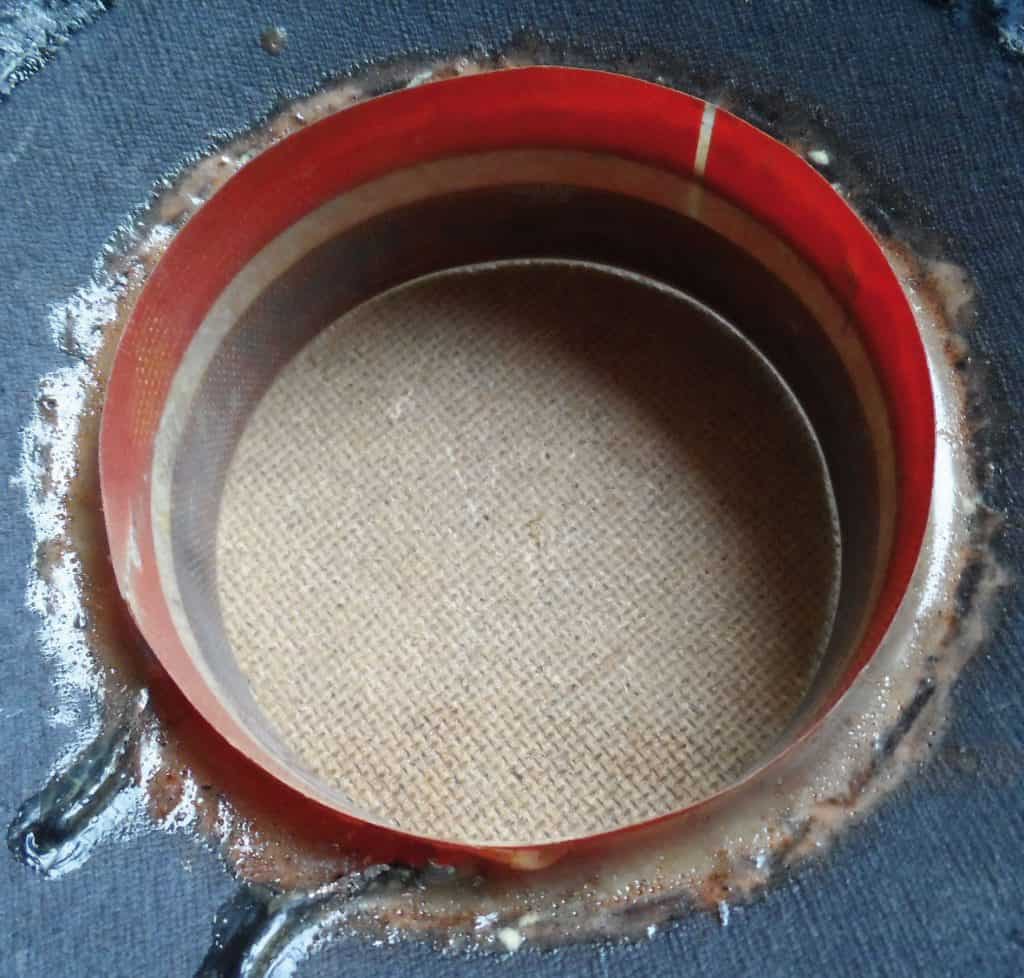
Fot. 3. Niefachowa próba mocowania cewki w membranie.
Dla kontrastu, na kolejnej fotografi (nr 4) widać prawidłowe mocowanie karkasu, przy użyciu jedynie minimalnej ilości kleju, i oczywiście jest to inny rodzaj spoiwa.
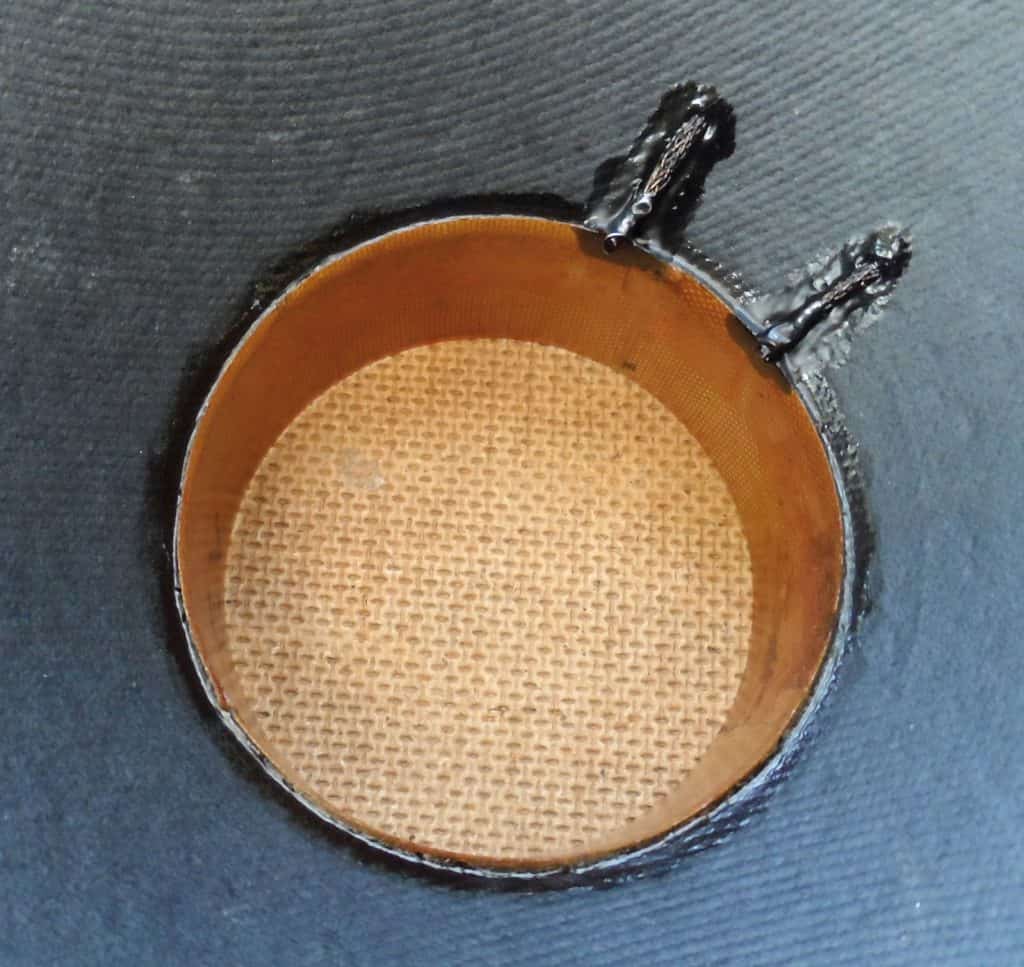
Fot. 4. Prawidłowo wklejona cewka jest elementem niedemontowalnym.
Z kolei nawijanie nowego uzwojenia na istniejący i wklejony w membranę karkas to równie marna sztuka, choćby z tego powodu, że prawidłowo wykonane uzwojenie wymaga wygrzania cewki w wysokiej temperaturze, o czym już wcześniej pisałem. Tak wykonana cewka, przy zachowaniu reguł prawidłowej eksploatacji głośnika, jest praktycznie wieczna, o czym przekonałem się wielokrotnie, gdy dostarczano do mnie głośniki nawet dwudziestoletnie, w których „skończyły się” membrany i zawieszenia, a po demontażu okazywało się, że cewka pozostała nienaruszona i wyglądała tak, jak tuż po opuszczeniu fabryki.
Na fotografii nr 5 pokazuję kilka takich cewek zdemontowanych ze starych głośników, które trzymam w warsztacie – choćby dla kontrastu z tymi, które uległy awarii w czasie nieporównanie krótszym i które są produkowane współcześnie.
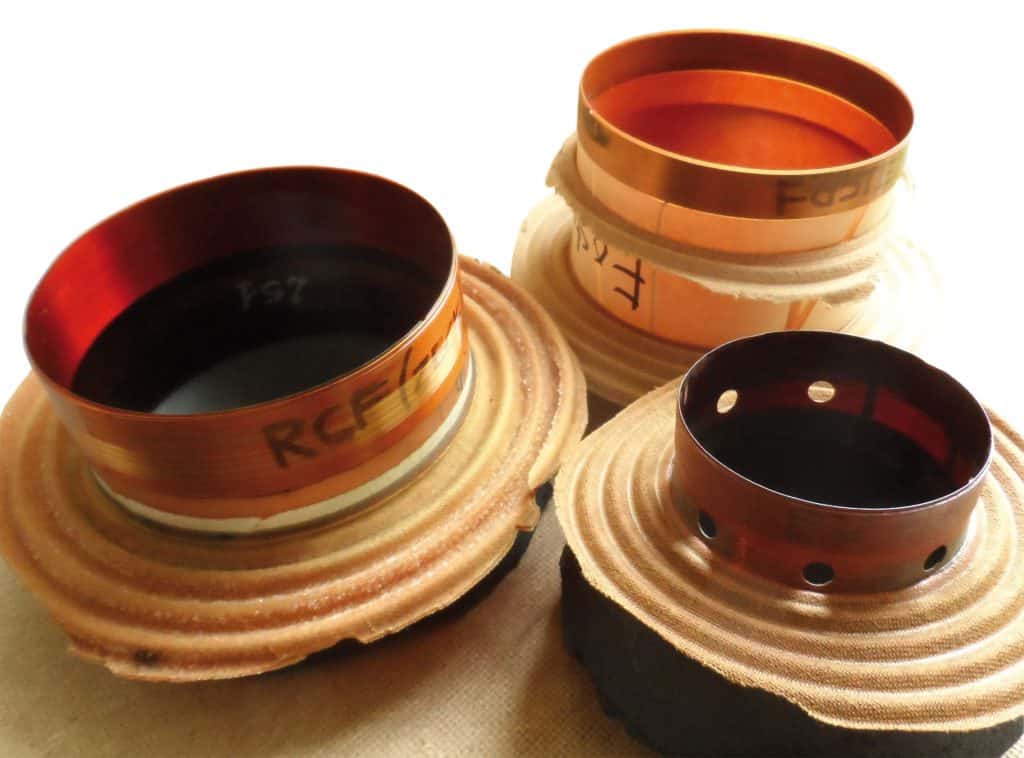
Fot. 5. Profesjonalne cewki przy prawidłowej eksploatacji są w zasadzie niezniszczalne i mogą zachować pełną sprawność przez kilkanaście i więcej lat.
Kiedy w swoim czasie zaglądałem na różne specjalistyczne fora internetowe, to z przerażeniem (ale i z rozbawieniem) czytałem, jak to domorośli specjaliści łączą uzwojenia klejem typu distal, co ma taką zaletę, że nie trzeba go wygrzewać, ale również i dość poważną wadę, bo ten klej po prostu roztopi się w wysokiej temperaturze, gdyż traci swoje właściwości spajające już powyżej 90°, a cewki głośnikowe w roboczych warunkach pracy potrafią się rozgrzewać się do znacznie wyższych temperatur, o czym wspomnę jeszcze w dalszej części artykułu.
Wracając jeszcze na chwilę do tematu klejenia, jako ciekawostkę mogę podać, że do zmontowania głośnika jako całości wykorzystuję sześć różnych rodzajów kleju: do impregnacji materiału na karkas, do uzwojenia cewki, do wklejania cewki w membranę, do łączenia membrany z resorami i wreszcie do montażu membrany i zawieszeń do kosza, oraz wspomniany w poprzednim odcinku klej do łączenia ferrytu z nabiegunnikami. Do tego dochodzi jeszcze specjalny impregnat do zawieszenia górnego, który spełnia ważną rolę, gdy chodzi o jego o prawidłową pracę i niezmienność parametrów w czasie.
Karkasy cewek – element trochę niedoceniany, a niesłychanie istotny
Uzwojenie to jedno, ale przecież trzeba je nawinąć na karkas, choć produkowane są również cewki bezkarkasowe, ale nie będą one tutaj omawiane. Ten element również stosunkowo często zawodzi, więc cewki profesjonalnych głośników wykonywane są przeważnie na karkasach z włókna szklanego (fiberglass), który to materiał ma bardzo wysoką odporność na temperaturę, dużą wytrzymałość mechaniczną i jest obojętny z punktu widzenia elektromagnetycznego. Istnieje również tworzywo o nazwie kapton, ale jego tańsze wersje potrafią spuchnąć pod wpływem wysokiej temperatury, co oczywiście powoduje destrukcję cewki. W ostatnich czasach pojawiło się jeszcze kilka innych materiałów z tworzyw sztucznych (nomex i podobne), ale te wymienione są z pewnością najpopularniejsze i najczęściej wykorzystywane, przy czym kapton jest najbardziej rozpowszechniony, głównie ze względu na łatwość jego aplikacji i stosunkowo korzystną cenę.
Na fotografii nr 6 pokazuję cewkę nawijaną właśnie na kaptonie (materiał półprzezroczysty) oraz dla porównania – cewkę wykonaną na karkasie z włókna szklanego.
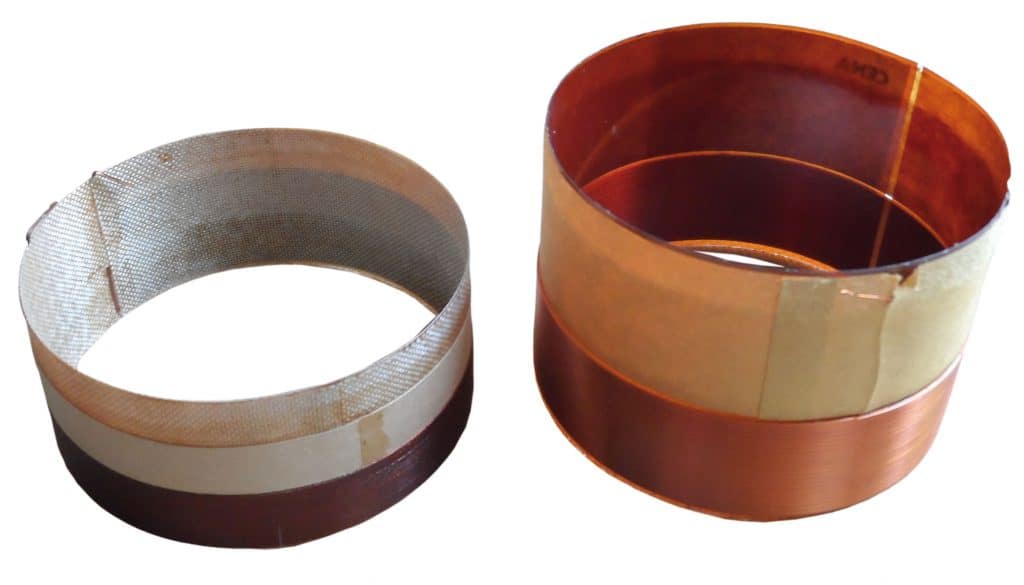
Fot. 6. Jako materiał na karkasy wykorzystuje się najczęściej tworzywo o nazwie kapton, w głośnikach najwyższej klasy stosowane jest przeważnie włókno szklane.
Z kolei samo włókno, jako materiał wyjściowy, zupełnie nie przypomina tego, z którego potem powstaje karkas, gdyż jest to zupełnie miękka, biała tkanina, która wymaga specjalnej obróbki, aby mógł z niej powstać sztywny karkas. Nie będę zagłębiał się w szczegóły technologiczne wykonywania takich karkasów, ale zapewniam, że jest to proces bez porównania bardziej pracochłonny niż wykorzystywanie każdego innego materiału w formie gotowej folii. Za to wykonany w ten sposób korpus cewki jest praktycznie niezniszczalny, na co dowodem jest choćby to, że trafiały już do mojego warsztatu głośniki, których uzwojenie było całkowicie spalone, a karkas pozostawał nienaruszony.
Na zdjęciu nr 7 pokazuję tkaninę szklaną i jako przykład gotowego karkasu na tej samej fotografii możecie Państwo obejrzeć cewkę o średnicy 4″, nawiniętą drutem płaskim na sztorc.
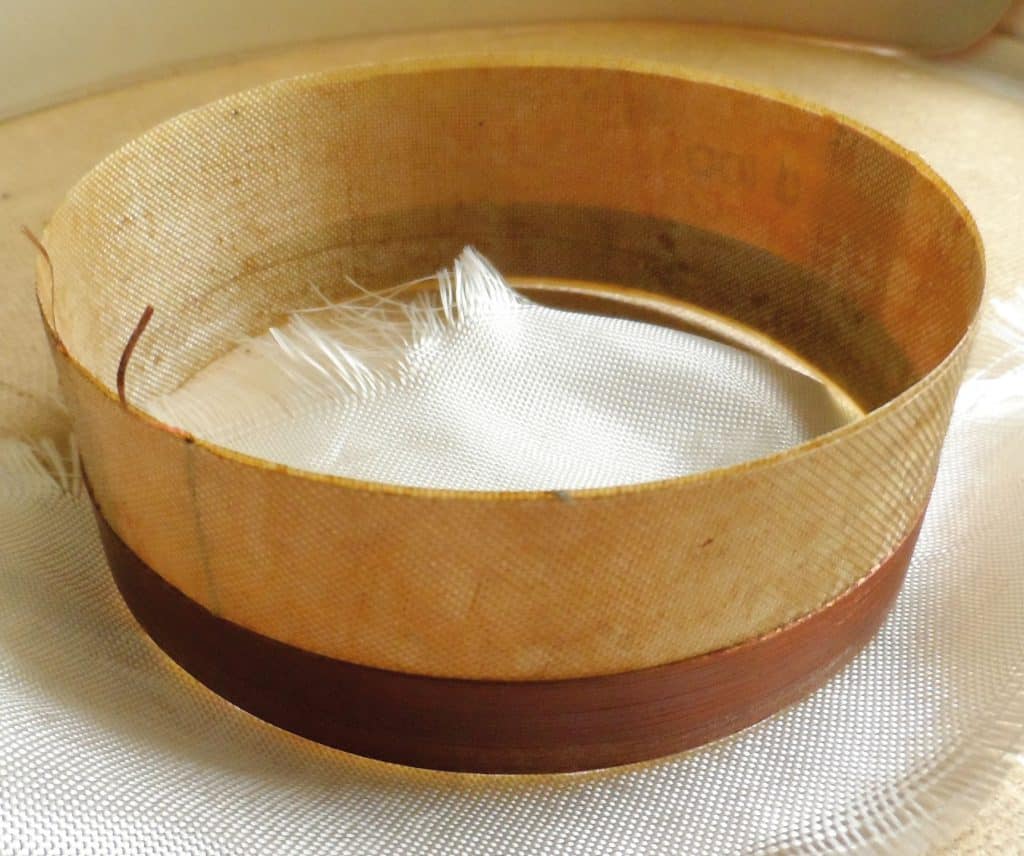
Fot. 7. Na zdjęciu widać włókno szklane i wykonany z niego karkas cewki nawiniętej drutem płaskim na sztorc.
Warto dodać, że jest to uzwojenie najtrudniejsze do wykonania i wymaga specjalnego oprzyrządowania oraz nietypowego drutu nawojowego o przekroju prostokątnym, co oczywiście powoduje, że taka cewka jest wielokrotnie droższa niż standardowa. Dlatego obecnie wiele firm ucieka od tej technologii na rzecz cewek dwustronnych, choć nadal jest ona powszechnie stosowana w przypadku głośników wysokotonowych, gdzie w zasadzie jest niemal standardem i to nawet wśród przetworników ze średniej półki cenowej.
Obecnie tylko w najtańszych głośnikach małej mocy (i czasem w sprzęcie gitarowym) stosuje się korpusy cewek wykonywane z impregnowanego papieru, a jeszcze jednym materiałem wykorzystywanym do tego celu jest folia aluminiowa, której główną zaletą jest to, że ma dobrą przewodność cieplną. Żeby zamknąć ten rozdział, dodam jeszcze, że karkasy nie powinny być zbyt wysokie w stosunku do wysokości uzwojenia, a stosunkowo często miewam do czynienia właśnie z taką wadą fabryczną. Dzieje się tak na przykład w sytuacji, gdy producent (lub naprawiacz) nie dysponuje odpowiednio głęboką membraną, co wymusza stosowanie karkasów o nienaturalnie dużej wysokości. Zbyt długi karkas utrudnia poprawne centrowanie, wprowadza niepotrzebną, dodatkową masę i generalnie jest błędem w sztuce, a taki błąd możecie Państwo obejrzeć na fotografii nr 8, gdzie wyraźnie widać uszkodzenie aluminiowego karkasu, którego długość jest ponad dwukrotnie większa niż wysokość uzwojenia.
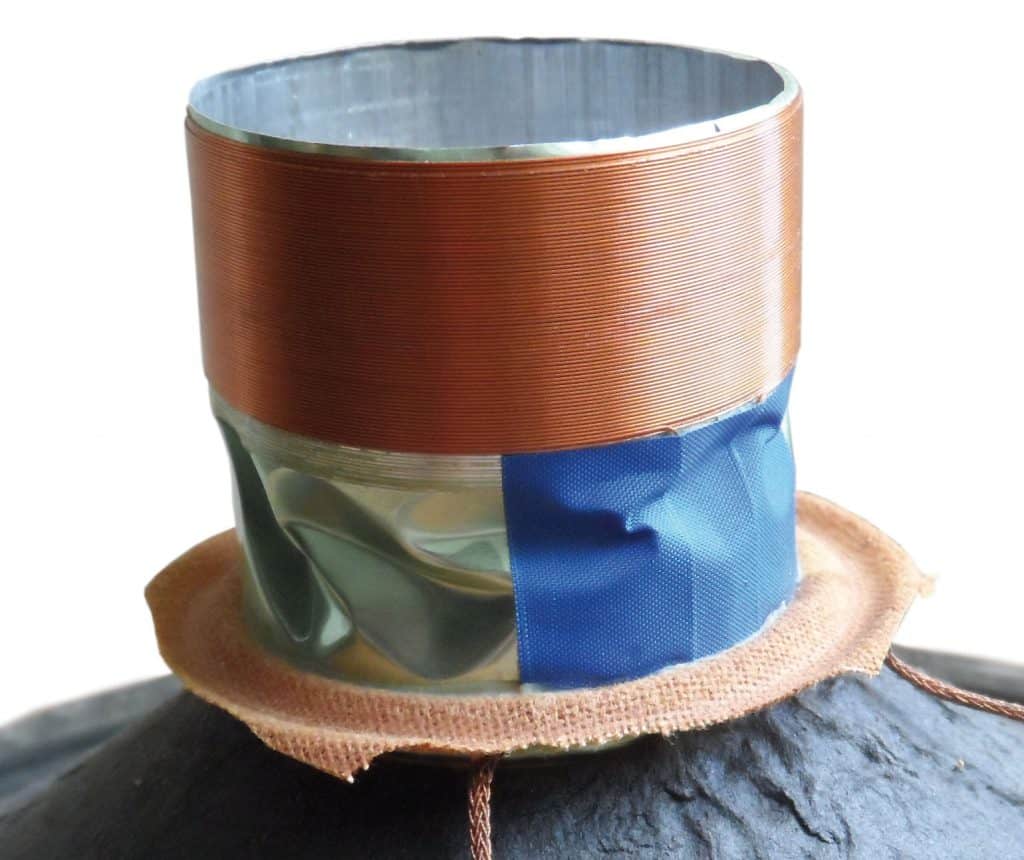
Fot. 8. Zbyt długi karkas to typowy błąd w sztuce, nie do zaakceptowania w fabrycznie nowych głośnikach.
Warto też pamiętać o tym, że zbyt wysokie uzwojenie co prawda zwiększa amplitudę liniowej pracy przetwornika, ale z drugiej strony osłabia jego skuteczność i powoduje, że cewka łatwiej może ulec uszkodzeniu, gdy skrajne zwoje będą w czasie pracy wychodzić poza pole magnetyczne. Dlatego zawsze należy dążyć pod tym względem do rozsądnego kompromisu, a już zupełnie niedopuszczalne jest przenoszenie standardów stosowanych w technice domowej Hi-Fi do głosników estradowych, o czym część producentów i osób zajmujących się naprawami głośników zdaje się zapominać.
Rozmiary cewek, czyli o niejednoznaczności standardów
Teraz poświęcę trochę miejsca na omówienie kwestii standardowych rozmiarów cewek i, jak się Państwo przekonacie, „standard” w tym wypadku wcale nie jest tak jednoznacznym pojęciem, jakby się mogło pozornie wydawać. Wiadomym jest, że średnica cewki to jeden z czynników determinujących moc głośnika, a wynika to z faktu, że ze zwiększaniem mocy musi wiązać się zwiększanie średnicy drutu nawojowego. To z kolej powoduje, że dla uzyskania standardowych impedancji (4, 8, 16 Ohm) musimy przy grubszym uzwojeniu zwiększać jego długość, a więc i obwód karkasu cewki. Opracowano więc standardowy typoszereg takich średnic i większość producentów trzyma się tych kilku podstawowych wymiarów, choć oczywiście bywają wyjątki. Ale czy mając, dajmy na to, głośnik z cewką 3″ produkcji firmy X, możemy zastąpić ją cewką firmy Y o identycznej nominalnej średnicy?
Na tak postawione pytanie jest tylko jedna prawidłowa odpowiedź: nie ma takiej możliwości. Praktycznie nie zdarza się bowiem, żeby cewki różnych producentów miały co do dziesiątych części milimetra identyczne rozmiary, a taka precyzja jest konieczna, żeby dokonać wymiany. Poza tym, występują różnej wielkości szczeliny, różnej grubości i długości karkasy i różne typy uzwojeń o zróżnicowanej wysokości, więc niestety, są to elementy całkowicie niezastępowalne. Czasem są to różnice rzędu dziesiątych części milimetra, ale bywa, że dochodzą do kilku milimetrów. Podam ekstremalny przykład dla cewki o nominalnej średnicy 100 mm (4″). Popularny głośnik pewnej amerykańskiej firmy ma trzpień o średnicy 98,7 mm, a głośnik innej legendarnej firmy z USA ma trzpień o średnicy 104 mm. Jak więc widzimy, mimo że oba mają standardową cewkę 4”, to faktyczna różnica w wymiarach wynosi ponad 5 mm. Dlatego otwiera się w tym zakresie szerokie pole do popisu dla rzemieślników, bo nie każdego klienta stać na zakup oryginalnego kompletu naprawczego, a nawet jeśli go nabędzie, to jeszcze nie oznacza, że będzie w stanie wymienić go samodzielnie. Jeśli chodzi o wykonanie cewki, to oprócz odpowiedniej średnicy i jakości drutu nawojowego, kleju i materiału na karkas, musimy dysponować metalową tuleją do nawinięcia cewki i bywa tak, że dla jednego standardowego wymiaru cewki gromadzi się tych elementów w warsztacie kilka czy nawet kilkanaście, a jeśli uwzględnimy wiele spotykanych średnic i wielu producentów, to z czasem ich liczba może dochodzić do kilkudziesięciu i więcej sztuk.
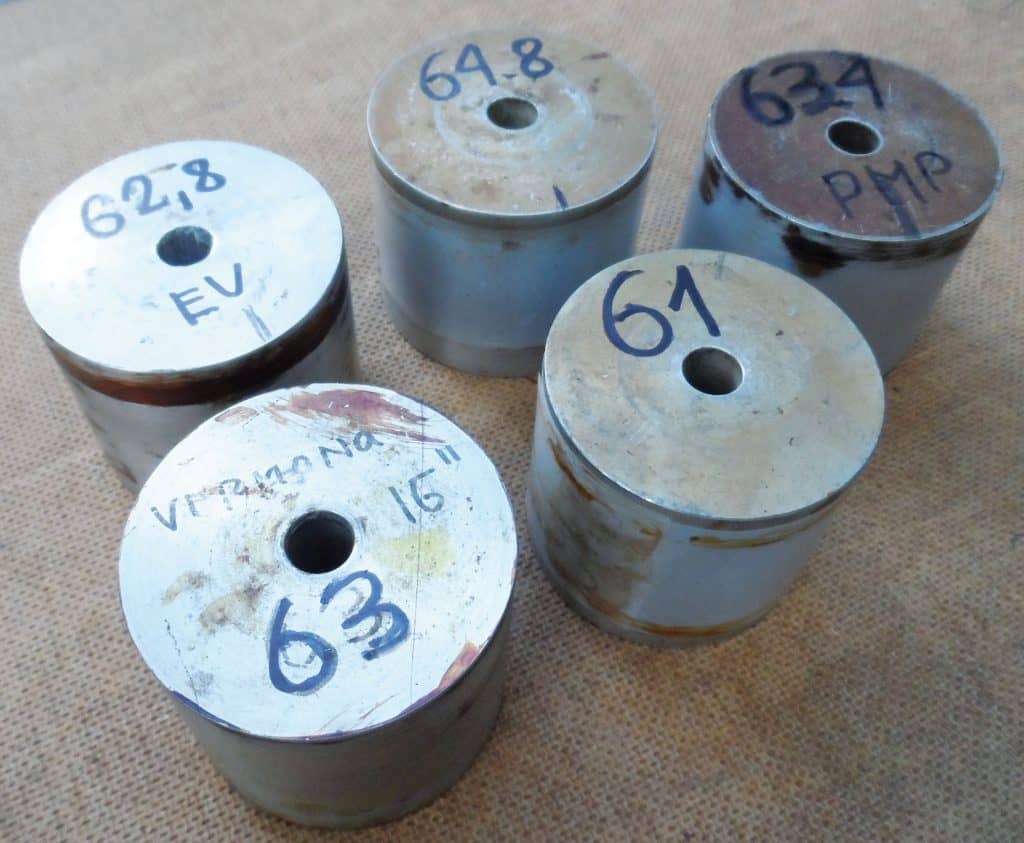
Fot. 9. Oprawki do nawijania cewek o średnicy nominalnej 2,5”.
Wysoka temperatura, czyli o odprowadzaniu ciepła z cewek
Chłodzenie cewki to bardzo istotna kwestia przy projektowaniu głośnika; obecnie firmy wykorzystują kilka metod odprowadzania z nich ciepła. Wykonywane są na przykład duże, centralne otwory w trzpieniu obwodu magnetycznego, nawierca się również szereg mniejszych otworów w nabiegunniku na obwodzie cewki, a także wentyluje się same kosze poprzez wykonanie w nich odpowiednich otworów lub kanałów.
Warto przy okazji wspomnieć, że głośnik dynamiczny ze swej natury ma bardzo małą sprawność, w sensie przetwarzania dostarczanej energii na falę dźwiękową. W przypadku klasycznych głośników membranowych ta sprawność to zaledwie około 3%, a reszta energii zamienia się właśnie w ciepło. Dlatego nie jest niczym dziwnym, gdy po koncercie albo po całonocnej pracy w dyskotece stalowe nabiegunniki dużych głośników potrafią niemal parzyć. Łatwo sobie wyobrazić, jaka temperatura panuje wewnątrz obwodu, czyli tam, gdzie pracuje cewka.
A jeśli ktoś ma słabą wyobraźnię, to może zerknąć na wykres (fot. 11) obrazujący wykres temperatury cewki w zależności od dostarczanej do niej mocy, który znalazłem w danych katalogowych publikowanych na stronie znanego producenta.
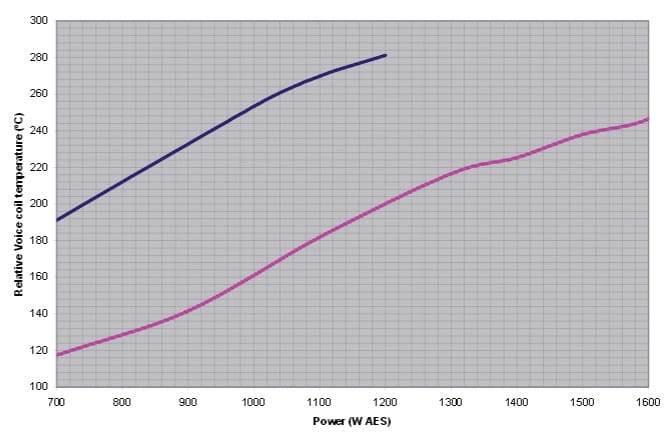
Fot. 11. Wykres temperatury cewki w zależności od wydzielanej w niej mocy na przykładzie dwóch modeli głośników znanego producenta.
Pokazane są dwa podobne głośniki, różniące się jednak zastosowanym systemem chłodzenia. Nie chcę komentować skrajnych wartości, jakie pokazane są na tym wykresie przy maksymalnej mocy przetwornika, bo na przykład standardowe druty nawojowe dostępne na rynku mają izolację o wytrzymałości 200°, a maksymalnie jest to 220°, a taką temperaturę głośniki w załączonej tabelce uzyskują na połowie swojej mocy nominalnej. Widać jednak wyraźnie, że powyżej mocy około 700 W przechodzimy już raczej w obszary abstrakcji i być może dlatego rozsądniej, a na pewno bezpieczniej, byłoby uznać, że 1 kW to raczej koniec możliwości mocowych nawet najlepszych głośników, bo praw fizyki nie da się przeskoczyć.
Bardzo dobrym sposobem zwiększającym wytrzymałość temperaturową cewki jest nawinięcie uzwojeń po obu stronach karkasu, co osobiście wykonywałem już w ubiegłym wieku, bo to dość stary patent, i tak wykonaną cewkę również można zobaczyć na fotografii nr 10.
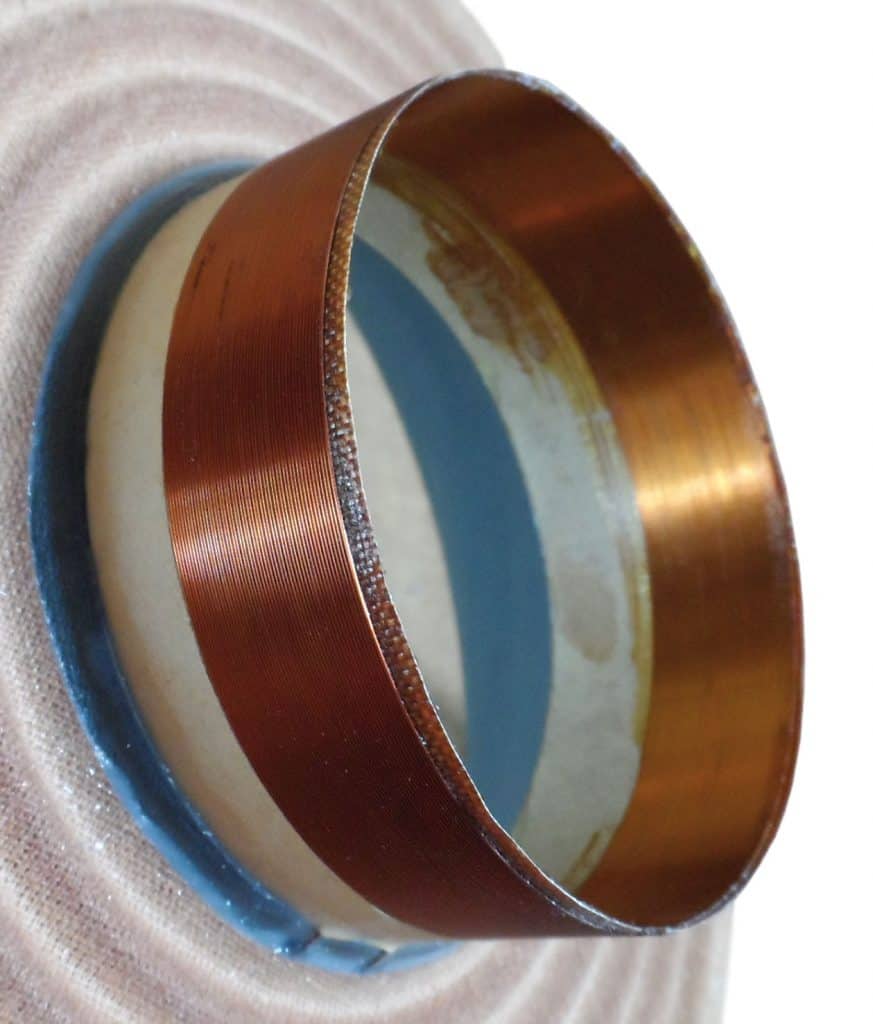
Fot. 10. Cewka nawijana po dwóch stronach karkasu jest znacznie bardziej odporna na wysokie temperatury.
Obecnie jest to technologia mocno promowana przez wielu czołowych producentów, gdyż nominalne moce głośników próbują nadążyć za lawinowym wzrostem mocy wzmacniaczy, co jest zadaniem w zasadzie niewykonalnym, gdyż istnieje pewna graniczna bariera mocy, której przekroczyć się nie da. Jednak próbuje się szukać bardziej skutecznych sposobów chłodzenia uzwojeń i cewki nawijane dwustronnie (inside/outside) są właśnie przykładem takich rozwiązań.
Klasyczna cewka nawijana jest najczęściej dwuwarstwowo, po jednej stronie karakasu, co powoduje, że pierwsza warstwa ma znacznie gorsze warunki chłodzenia. Nawijając taką samą ilość drutu (czyli dwa uzwojenia) po jego obu stronach, stwarzamy im identyczne warunki odprowadzania ciepła i dlatego moc tak wykonanej cewki rośnie, przy zachowaniu identycznej średnicy drutu nawojowego. Oczywiście ta moc nie może rosnąć w nieskończoność i dlatego wiele firm, określając moc głośników, ucieka się do różnych zabiegów o charakterze marketingowym, co zresztą trochę przypomina wielokrotnie opisywaną przeze mnie sytuację z definiowaniem mocy współczesnych wzmacniaczy.
Warto zapamiętać i przyjąć za pewnik, że podstawą niezawodnej pracy cewki głośnikowej jest zastosowanie drutu nawojowego o jak największej odporności termicznej izolacji, użycie właściwego spoiwa do klejenia uzwojeń, odpowiedniego materiału na karkas i oczywiście staranność i precyzja jej wykonania, łącznie z procedurą wklejenia w membranę, gdzie najmniejsze odchylenie od pionu skutkuje brakiem możliwości poprawnego wycentrowania. Bardzo ważną kwestią jest również sposób wyprowadzenia sztywnego drutu nawojowego z cewki i połączenia go z miękką linką, przekazującą prąd z zacisków głośnika. Szczególne problemy stwarzają cewki nawijane drutem aluminiowym, a jeszcze większe, jeśli jest to uzwojenie wykonane drutem płaskim na sztorc. Bywa tak, że właśnie w tym miejscu następuje przerwa na skutek drgań i głośnik nie gra, choć nie doszło do żadnej ewidentnej awarii. Takie cewki najczęściej spotykamy w driverach średnio- i wysokotonowych i dlatego tych głośników się nie naprawia, tylko wymienia komplety naprawcze zakupione u producenta lub u „chińczyka”. Inna sprawa, że często jest to ta sama fabryka, a różnica polega wyłącznie na cenie i na kanałach dystrybucji.
Przykład zwiększenia mocy starego głośnika wykorzystujący nowoczesną technologię
O tym, jak istotna jest technologia wykonania cewki, niech świadczy fakt, że tylko dzięki lepszym materiałom i nowocześniejszej technologii można czasem uzyskać wielokrotne zwiększenie mocy nominalnej głośnika przy wykorzystaniu tego samego obwodu magnetycznego. Przykładem niech będzie stary, ale popularny w dawnych czasach głośnik Vermony o oznaczeniu L 3702. Ma on trochę nietypową średnicę, bo 16” i oryginalnie miał membranę z papierowym górnym zawieszeniem (jak w głośnikach gitarowych) i cewkę o mocy nominalnej jedynie 50 VA, mimo że ma ona całkiem sporą średnicę, bo 2,5″.
Ponieważ w swoim czasie sporo tych głośników było w użyciu i często trafiały do mnie do serwisu, postanowiłem wykonać specjalnie dla tego modelu zupełnie inną niż oryginalna membranę, z górnym zawieszeniem wykonanym z impregnowanej tkaniny, oraz oczywiście znacznie wytrzymalszą cewkę. Okazało się, że po wymianie całego układu drgającego głośnik nabrał takiego wigoru i grał tak dobrze, że przywożono do mnie nawet fabrycznie nowe egzemplarze z prośbą o przeróbkę. Gwarantowałem dla tego głośnika 200 W mocy RMS i do dziś wiele tych vermon jest w użyciu, dlatego pokazuję na zdjęciu nr 12 właśnie taki głośnik w widoku od strony magnesu, a także oddzielnie membranę z zawieszeniami i wklejoną cewką.
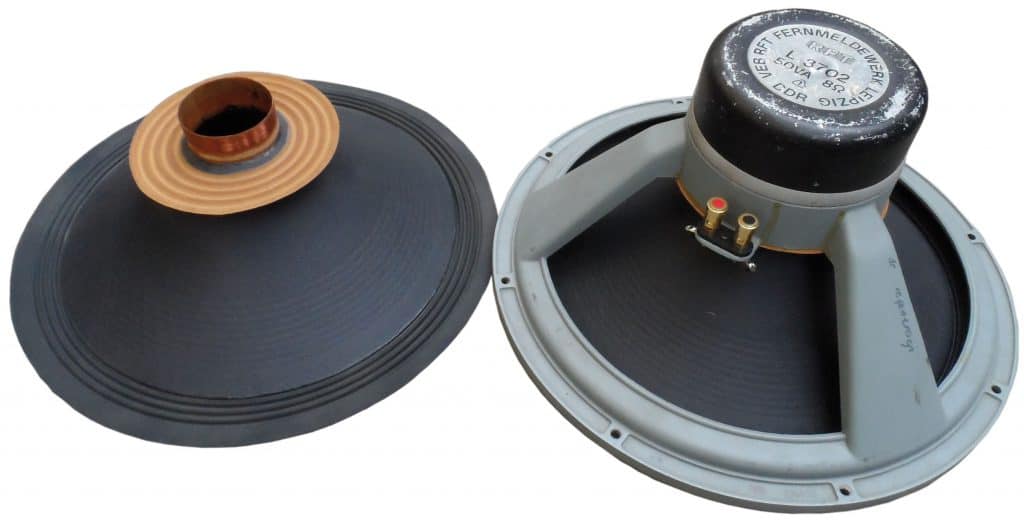
Fot. 12. Przykład modernizacji i zwiększenia mocy starego głośnika poprzez zastosowanie nowoczesnej technologii.
Przy użyciu tej samej cewki o średnicy 2,5” można by uzyskać jeszcze większą moc, gdyby obwód magnetyczny miał wentylację, ale sytuację w tym wypadku ratuje w pewnym stopniu zamontowanie kołpaka osłonowego cewki, wykonanego z materiału przepuszczającego powietrze (w przeciwieństwie do papierowego, który takich właściwości nie ma). Za to w magnesach wentylowanych kołpak papierowy jest wręcz niezbędny, bo właśnie dzięki temu, że nie przepuszcza powietrza, może wymuszać dodatkowy jego ruch w szczelinie, a poza tym, dodatkowo usztywnia membranę w jej dolnej części. Dlatego często takie papierowe kołpaki mają bardzo duże średnice, większe, niżby to wynikało z rozmiaru cewki, którą osłaniają. Jak więc widać na podanym przykładzie, czasem nie warto złomować starszego sprzętu – w przypadku niektórych głośników jest to wręcz zbrodnia, choćby z uwagi na stosowane w niektórych starszych modelach komponenty bardzo dobrej jakości, za które w dzisiejszych czasach musimy bardzo słono płacić. Muszę jednak wyraźnie podkreślić (bo jestem o to często pytany), że tylko nieliczne głośniki warto w ten sposób modyfikować, a wynika głównie z przyczyn ekonomicznych. O ile bowiem starsze przetworniki renomowanych producentów były niejednokrotnie lepiej wykonywane i z lepszych materiałów niż nowe (mające często taką samą firmową nazwę), o tyle popularne głośniki klasy budżetowej tych samych firm, które przeniosły swoją produkcję na Daleki Wschód, często w ogólne nie kwalifikują się do naprawy, a jeśli nawet, to koszty kompletnego remontu mogą być wyższe niż cena nowego głośnika. Z punktu widzenia osoby wykonującej taką usługę jest zupełnie obojętne, czy remontuje głośnik za 200, czy za 1000 zł. Wiem, że są na rynku głośniki jeszcze o wiele tańsze, ale ja się takimi wyrobami w ogóle nie zajmuję. Wkład pracy jest identyczny, a trudno raczej celowo użyć gorszych materiałów i mniej się przyłożyć, tylko dlatego, że klient kupił głośnik za grosze na bazarze albo w jakiejś firmie, która kleci je z przypadkowych zespołów kupionych u „chińczyka”.
Naprawiać czy nie?
W tym miejscu, niejako tytułem podsumowania, dość łatwo przywołać analogię z szeroko rozumianą elektroniką w rodzaju mikserów, wzmacniaczy itp. W tej kategorii też przecież występują na rynku wyroby jednorazowego użytku albo, inaczej mówiąc, takie, których naprawa jest zupełnie nieopłacalna – i dokładnie tak samo wygląda sytuacja z głośnikami.
Z tego miejsca zapraszam do następnego numeru MiT, gdzie w trzeciej (i chyba już ostatniej) części artykułu zajmę się membranami, zawieszeniami i wszystkim tym, czego nie udało się zmieścić w dwóch pierwszych odcinkach.
Piotr Peto, Muzyka i Technologia
————————————————————————————————————————————————-
Budowa i serwisowanie głośników – kosze i obwody magnetyczne
Niewątpliwie niezbędnym – i kto wie, czy nie najważniejszym elementem każdej aparatury nagłaśniającej – są przetworniki elektroakustyczne, czyli mówiąc popularnym językiem: głośniki. To one w znacznym stopniu decydują o jakości brzmienia zestawu nagłaśniającego i to niezależnie od jego wielkości, mocy i miejsca, w którym będzie wykorzystywany. Na niewiele zdadzą się nawet najbardziej wymyślne konstrukcje paczek napędzanych supernowoczesnymi wzmacniaczami, z wykorzystaniem zaawansowanych procesorów głośnikowych, jeśli sygnał będzie finalnie trafiał do przetworników, w których pękają membrany, cewki odklejają się od membran, a uzwojenia od karkasów, pozostając w szczelinach obwodów na pamiątkę radosnej twórczości producenta lub majstra, który podjął się naprawy przetwornika, mając o tym jedynie bardzo blade pojęcie.
————————————————————————————————————————————————-
Budowa i serwisowanie głośników – membrany i zawieszenia
W dwóch poprzednich odcinkach cyklu o głośnikach omówiłem konstrukcję koszy, obwodów magnetycznych i cewek głośnikowych, dzisiaj zajmę się membranami i ich zawieszeniami, zwanymi również resorami, zapewne przez analogię do techniki samochodowej. Omówię pokrótce technologię produkcji tych elementów, a potem przejdę do części bardziej praktycznej, bo zdaję sobie sprawę z faktu, że większość czytelników to właśnie praktycy, dla których najistotniejsza jest wiedza pozwalająca na optymalne wykorzystanie posiadanego sprzętu.
————————————————————————————————————————————————-